Продукция предприятия "Полесье" популярна не только у белорусских детей, но и у малышей во многих странах мира. Например, пластмассовая бетономешалка с набором каменщика и самосвал с резиновыми колесами становились игрушками года в Польше, а последний еще и в Германии. Корреспондент Sputnik Дмитрий Босак отправился на фабрику и узнал, как производят всемирно известные игрушки.
От ручного станка к автоматизированному производству
История компании началась в 1998 году. Тогда коллектив из нескольких человек на единственном ручном выдувном станке выдал первую партию игрушек — это были пластиковые пирамидки.
За 19 лет штат сотрудников вырос до трех тысяч человек, компания начала выпуск игрушек под несколькими брендами.
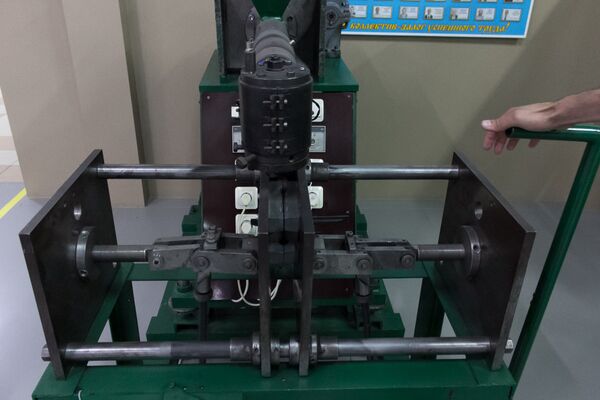
"Сейчас в нашем производственном цеху установлено современное оборудование от ведущих мировых производителей. Есть две технологии производства: литье под давлением и экструзия с раздувом", — рассказывает начальник отдела маркетинга Андрей Марчук, проводя экскурсию по предприятию.
Сегодня в производстве задействован 121 станок. Это термопластавтоматы Demag, Engel, Arburg, робототехнический комплекс Wittmann, централизованная система подачи материала Koch.
Производством пресс-форм на фабрике занимается инструментальный цех. Большой пласт металла обрабатывается и вытачивается на токарном станке. В итоге получается две части пресс-формы: матрица и пуансон. В процессе производства они смыкаются, и в свободное пространство вплавляется пластик — так образуется необходимая деталь игрушки.
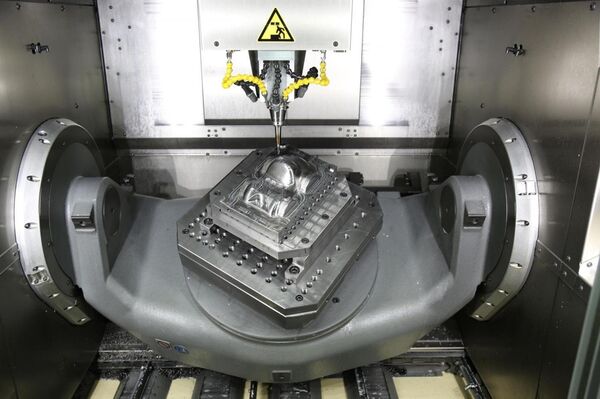
"У нас есть пресс-формы, которые работают фактически с момента основания. Тот же конструктор "Строитель" выпускался еще 19 лет назад и до сих пор выпускается. Со временем мы усложняем игрушку, добавляем новые элементы и детали, чтобы она не теряла свою актуальность и была интересна детям", — говорит Андрей.
Инструментальный цех оборудован станками японской Mitsubishi и американской Haas. Использование современных технологий при изготовлении пресс-форм позволяет добиваться точности до 5 микрон — это в 60 раз тоньше тетрадного листа.
"Сборочный цех по численному составу — самое большое подразделение. Здесь работает более тысячи человек. Основное подразделение располагается в Кобрине, а дополнительное функционирует в Пинске. Его специально организовали, чтобы усилить производство, ведь сборка готового изделия — это достаточно трудоемкий процесс, так как все элементы нужно соединить вручную", — объясняет собеседник.
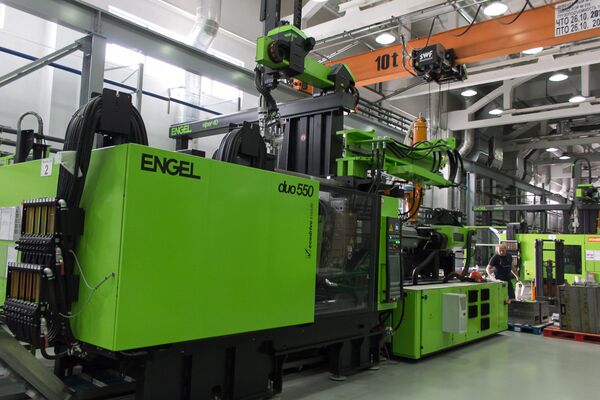
Взрослые знают, что нужно детям
Ассортимент игрушек постоянно пополняется. Специалисты предприятия анализируют рынок и пожелания основных потребителей — детей и их родителей. Игрушка должна быть не просто красивой и функциональной. Главный акцент делается на ее безопасность, на втором месте — ее развивающая сторона.
"Естественно, когда в каталоге более двух тысяч артикулов, добавление каждого нового — это взвешенный шаг. Произвести игрушку достаточно трудоемкий процесс, требующий много времени и ресурсов. Самая простая пресс-форма предполагает большие затраты на ее изготовление. Если игрушка сложная и состоит из 10-15 пресс-форм, цена их выпуска, соответственно, увеличивается", — делится сотрудник "Полесья".
Поэтому перед тем как запустить какое-либо изделие в массовое производство, его проект проходит длительную стадию разработки и корректировки. Прототип предварительно выращивается на 3D-принтере.
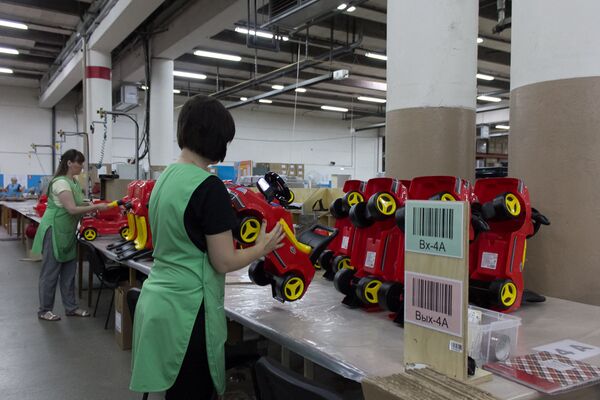
"Стоимость ошибки на данном этапе еще маленькая. Естественно, в процессе работы выясняются какие-то нюансы, недочеты, и они исправляются. Это позволяет существенно экономить ресурсы", — поясняет начальник отдела маркетинга.
Безопасность — не игрушка
Вся продукция, производимая фабрикой "Полесье", соответствует требованиям директив безопасности Евросоюза. Пластик, из которого сделаны игрушки, полностью безопасен, заявляют производители. Предприятие использует красители, которые разрешены к контакту с пищевыми продуктами. Фактически из этого пластика можно производить посуду. Аллергии на него не будет.
"Не всегда покупатель обращает внимание на то, что, допустим, на машинке стоит ограничение от трех лет. Если игрушка нравится, ее ребенку все равно покупают. А маленьким детям все надо попробовать на зуб", — говорит Андрей.
Не так давно компания начала производить погремушки для малышей.
"Клеем их склеивать нельзя, поэтому мы соединяем элементы в них с помощью ультразвука. Погремушка получается максимально безопасной, никаких вредных материалов не используется", — делится Андрей.
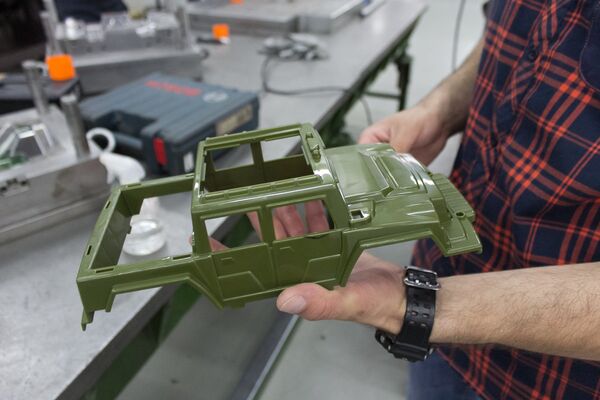
Выбор родителей зависит от менталитета
Сегодня в ассортименте предприятия более двух тысяч позиций. Он включает практически все группы пластмассовых игрушек для детей: конструкторы и транспорт, игровые комплексы и развивающие игрушки, детские велосипеды и квадроциклы, посуду и мебель для кукол, товары для активного отдыха и многое другое для досуга всей семьи.
От менталитета людей в определенной стране зависит популярность какой-либо продукции. Например, в Европе пользуются спросом наборы строительных инструментов, а также специализированные игровые комплексы, в то время как в СНГ выбор делается в пользу автомобилей, летних наборов и логических игрушек.
"Менталитет отличается. В Европе, например, очень гордятся тем, что дедушка был фермером, отец фермер — и я буду. Там люди работают в какой-либо сфере из поколения в поколение. Поэтому те же бетономешалки, какие-то специализированные игрушки в виде наборов касок и стройинструментов намного лучше продаются там. За счет таких, казалось бы, не связанных с игрушками отличий, формируется спрос и на нашу продукцию", — считает начальник отдела маркетинга.
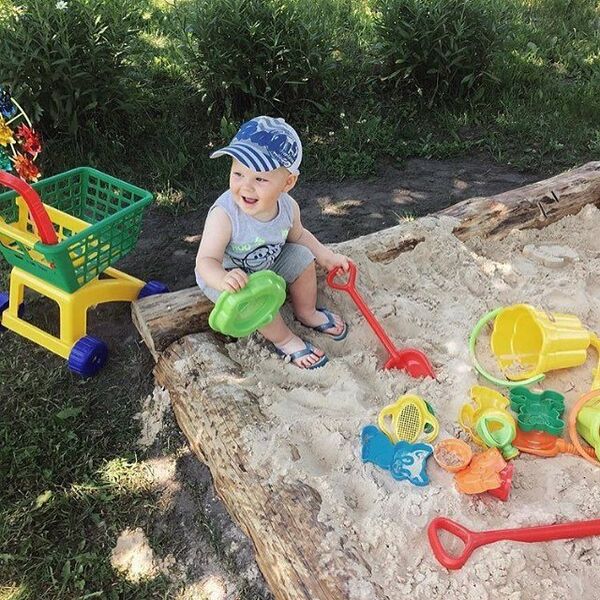
Кроме того, в европейских странах принято, что до определенного возраста дети изучают только базовые цвета, которые сложно перепутать с другими: красный, зеленый, синий, желтый. А уже цвета, которые образуются при смешении нескольких, появляются в жизни детей позже.
"На первой стадии развития ребенка, ему очень сложно воспринимать, например, розовый или фиолетовый. Они достаточно сложные и непонятные для него. Поэтому мы делаем ставку на стандартные цвета, чтобы на примере во время игры можно было научить ребенка цветам", — говорит Андрей.